What is Total Quality Management?
Table of Contents
Customer expectations are rising. Modern clients are well aware of the potential of today's technology. They want corporations to use that influence to provide the highest quality service and products.
Total quality management - tqm full form is the ongoing process of recognizing, decreasing, or eliminating faults in manufacturing. It streamlines supply chain management, enhances the client experience, and guarantees that personnel receive adequate training.
Total quality management aims to keep all stakeholders involved in the manufacturing process accountable for the overall quality of the final product or service. It can help firms fill in the gaps and keep a grasp on quality while pushing their speed to the limit. In this article, we will discuss all in detail about it.
Understanding the meaning and concept of Total Quality Management
To fully comprehend the idea of "total quality management - tqm full form, let us first define quality.
Quality is a criterion that determines the quality or inferiority of a product or service. Quality can be described as an attribute that distinguishes one product or service from its competitors. Quality is vital in every business. To thrive in today's competitive environment, business marketers must prioritize brand quality over quantity.
It can be said that tqm meaning is a structured approach to organizational management. The process aims to increase the quality of an organization's outputs, such as goods and services, by continuously improving internal practices. The tqm approach's standards can reflect both internal priorities and existing industry norms.
Industry standards can be developed at multiple levels, including aligning with numerous laws and regulations governing the everyday operations of a certain business. Industry standards can also include the production of goods by established standards, even if the norm is not supported by official legislation. Acceptance sampling can be utilised for assessing progress towards the TQM objective.
In other words, TQM meaning is described as a continual effort by both the management and staff of a certain firm to achieve long-term client loyalty and satisfaction. To gain loyalty from your clients, you must provide something extra. Durability, dependability, and usability are some of the ways quality can be judged.
It is a systematic effort by employees to continuously enhance the quality of their products and services through appropriate feedback and research. The obligation to ensure better product or service quality does not fall only on one individual.
Principles of Total Quality Management
Achieving this requires an intense concentration on the concepts of TQM:
Customers come first
TQM's first and most important pillar of success is an unbroken focus on the customer's experience throughout all contacts with the organization. From initial contact to purchase and ongoing assistance, the consumer should always be the top focus.
Employee involvement
TQM necessitates every team member's participation to ensure that complete quality control is provided at all levels. It does not focus on a particular department because the goal is to offer a positive experience for consumers at all levels of the organization.
Process-oriented
It focuses on developing and implementing processes that enable organizations to achieve and sustain success. Quantifying success and outlining the actions taken to get there are critical to the successful implementation of it.
System connectivity
TQM strategies focus on maximizing every asset accessible to the company. This is best accomplished through system integrations, which connect various business sections into a single, well-oiled machine that operates in perfect harmony.
Communication or relationship-based
It mandates that every team member perform to their full potential and contribute to the team's success. This means that communication and transparency are essential components of successful TQM processes.
Based on data
It does not use guesswork. Instead, data is used to develop the company, and decisions are based on quantifiable facts. This strategy assures that decisions are objective, dependable, and efficient. Leveraging data-driven insights enables firms to identify areas for improvement, set realistic goals, and precisely track progress. It encourages transparency and accountability.
Continuous improvement
It is not a one-time process. Perfection is impossible; thus, the organization should continually strive to get as close to it as possible. This entails using a QMS to establish clear, quantifiable goals, assessing performance, and making adjustments as needed. Continuous efforts develop a culture of excellence and drive long-term success, propelling the organization toward its strategic objectives.
Systematic flow
In TQM, systematic flow is the painstakingly ordered and sequential arrangement of processes to ensure smooth operation. Each step is carefully planned and executed to ensure consistency and minimize disturbance. This rigorous approach ensures superior control, predictability, and understanding of each process, resulting in higher quality and productivity.
These TQM pillars provide a context for all decisions made within the methodology. When your organization gets lost, these concepts serve as guiding stars to help you get back on track. Implementing TQM in your business involves making company-wide changes to know how work is done.
Importance of TQM
TQM can improve employee and organizational development. Companies can establish and maintain cultural norms that drive long-term success for both clients and the firm by requiring all employees to focus on quality management and continuous improvement. The quality-focused approach assists firms in identifying staff skill shortfalls, as well as the necessary training, education, or mentorship to address those needs.
TQM emphasizes teamwork, leading to the forming of cross-functional teams and knowledge exchange. Increased communication and coordination among disparate groups strengthen institutional knowledge and provide organizations with greater flexibility in staff deployment.
Implementation of TQM Principles and its Procedures
The general procedure of implementing tqm includes the following steps:
- The organization evaluates its current culture, quality management methods, and core values.
- Management decides to commit to tqm and creates a master plan.
- The company recognizes and prioritizes client wants.
- Management diagrams the procedures required to meet consumer needs.
- Management assembles a team to oversee all the work done and to increase the processes.
- Management begins to contribute to the process by conducting more planning and training.
- Management develops a method to standardize daily process management.
- Management solicits feedback from employees regularly.
Implementing TQM requires a long-term commitment, with planning, development, and implementation times varying in every organization.
Benefits of total quality management
Based on the usage and implementation, the following are the benefits of total quality management:
Minimal product defects
It aims to create products and services that are correct the first time. This means that items ship with fewer flaws, which reduces product recalls, future customer support costs, and product fixes.
Customers are satisfied
Customers are more satisfied when they receive high-quality products that fulfill their needs. High customer satisfaction can lead to greater market share and revenue growth through upselling and customer-led word-of-mouth marketing.
Innovative processes
TQM encourages organizations to research ongoing production issues to find effective solutions. As a result, companies typically design creative ways to eliminate difficulties. It may also assist them in developing measures to prevent similar problems from arising again. This can help to improve the quality of the items.
Increased employee morale
Meeting or exceeding client needs and achieving optimal results might benefit a company's personnel. They may feel included and valued because of their contribution to the product. This can help to enhance their morale, which can eventually lead to maintaining overall quality and increasing productivity at the organization.
Reduce expenses
Companies save money on customer assistance, product replacements, field service, and product repair since fewer product problems exist. The cost reductions trickle into the bottom line, resulting in improved profit margins.
Well-defined cultural values
Organizations that use TQM create and foster fundamental principles centered on quality management and continual improvement. The TQM attitude affects all elements of an organization, including hiring, internal operations, and product creation.
Other advantages
Other than those mentioned above, the following are also the benefits of total quality management:
- Increased job security: its stability and prosperity give employees more job security.
- Improved employee morale: TQM empowers employees, which boosts workplace morale and motivation.
- Enhanced shareholder and stakeholder value: it has a beneficial influence on performance and reputation and helps both stakeholders and shareholders.
- Improved and innovative processes: it creates an innovative culture, resulting in creative and successful procedures being implemented.
- Higher profitability: its impact on productivity, cost reduction, and customer satisfaction all help to boost profitability.
- Increased emphasis on customer satisfaction: it prioritizes client demands, resulting in products and services that exceed customer expectations.
- Increased client loyalty and retention: Satisfied Customers are more likely to stay loyal, resulting in long-term connections.
- Higher productivity: it improves processes and lowers waste, resulting in increased productivity and efficiency.
- Improved market image: Organisations that apply tqm obtain a positive reputation, which fosters trust and confidence in the marketplace.
Disadvantages of total quality management
- Planning and resources: it requires extensive planning and resources over time to be adequately devoted to the transformation.
- Company-wide dedication. Continuous improvement in TQM requires an organizational culture that focuses on process improvement. All management levels must be supportive.
- Additional expenses: it may increase training, infrastructure, and team development expenditures.
- Time: It may take years for an organization to achieve its planned results.
- Partial effort: Because of the effort required to carry it out in the organisation, an insufficient step during the process towards it may fail.
Essential requirements to check for when implementing TQM
Commitment
Quality development (in all aspects) must be everyone's responsibility inside the organization. Top management must demonstrate a clear commitment to remove all the barriers coming in the way of ongoing quality improvement and make the necessary efforts to create an atmosphere conducive to changing attitudes. Training and assistance for this should be expanded.
Culture
Proper training should be provided to achieve changes in attitudes and culture.
Continuous Improvement
Recognise improvement as a continual process rather than a one-time program.
Focus on Customers
Perfection in service with zero flaws and complete satisfaction for the end user, whether internal or external.
Control
Ensure monitoring and control checks are in place to detect any deviations from the intended implementation path.
The PDCA cycle for TQM
Planning phase
This is the most important phase in quality management. During this phase, employees must present their specific questions and problems that must be solved. Employees inform management of various issues they face in their daily operations and analyze the root cause of the problem. They must conduct the necessary study and gather significant data to help them solve all the challenges.
Doing phase
Employees generate solutions to the challenges outlined in the planning phase during the doing phase. Employee challenges are addressed through the development and implementation of strategies. The efficiency and efficacy of solutions and strategies are also assessed at this stage.
Checking Phase
During this phase, a comparison analysis of before and after is performed to analyze the effectiveness of the processes and measure the results.
Acting Phase
This is the final phase of the cycle, in which personnel document their results and ready themselves to confront additional challenges.
TQM is everybody's duty in the organization
TQM asks that all stakeholders accept responsibility for their roles, which includes both admitting fault and expressing credit. Accountability is required when working to improve product and service quality. When coping with mishaps and outages, quality management is about learning to win from failure.
Tracking metrics and comparing operational results before and after modifications is the most effective way to learn what works and what doesn't. Systems must also be established and followed so that success may be duplicated and enhanced. The improvement process should never be stagnant, ensuring the search for excellence never stops.
Conclusion
A successful TQM deployment necessitates extensive training for the people involved. Because the training program can divert employees' attention away from their daily tasks, it may have a detrimental short-term impact.
Furthermore, because total quality management tends to result in a continual succession of gradual adjustments, it may elicit an unfavorable reaction from employees who enjoy the old system or are frightened of losing their employment. It works best when management provides strong support and commitment.
People also search for
FAQs
What Can Total Quality Management Do?
TQM controls all activities and responsibilities necessary to maintain a desired level of excellence within a firm and its operations. This includes establishing a quality strategy, developing and implementing quality planning and assurance, as well as quality control and improvement strategies.
Where is TQM implemented?
TQM is utilized in various industries, including manufacturing, banking and finance, and medicine. It offers a unified vision for systemic change that prioritizes long-term transformation over short-term aims.
What is the background of TQM?
History of Total Quality Management. The term total quality management was first coined by the Naval Air Systems Command to characterize their Japanese-style management approach to quality improvement.
What is the role of leadership in Total Quality Management?
Effective tqm leaders can explain the value of quality to all employees and foster a shared sense of purpose. Empowering People and Promoting Employee Involvement: Leadership in tqm entails empowering people and encouraging active participation in the improvement process.
What is TQM execution?
Total quality management is a management approach to customer happiness, employee satisfaction, and supplier relationships. This emphasizes the importance of continually improving an organization's processes and infrastructure in order to provide high-quality goods and services.
How does TQM reduce error?
TQM necessitates the engagement of all employees during the production stage to ensure the overall quality of the final service or product. To eliminate errors, it employs internal process standards and recommendations.
Why is TQM efficient?
It provides quality assurance that consumers will receive what they anticipate, as well as a method for dealing with dissatisfied customers, making necessary improvements, and preventing similar reoccurrences.
Modify your HR and payroll tasks with factoHR today
Let your HR and workforce focus on most important business decisions while factoHR can reduce the burden of daily activities of the organization.
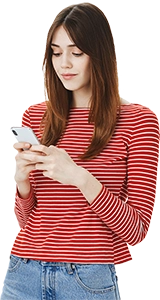
© 2025 Copyright factoHR